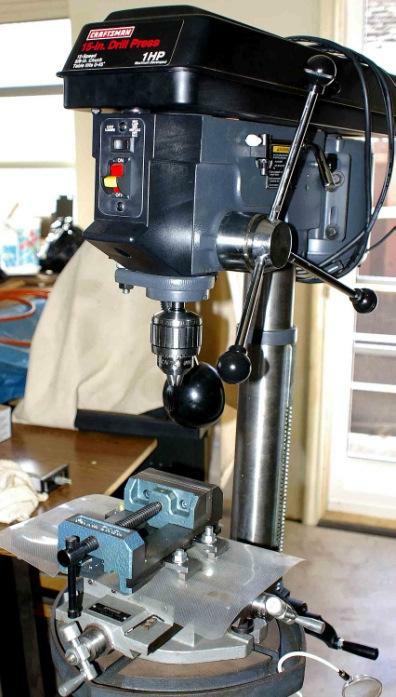
This is another excellent article by Mikey, a frequent contributor to MachinistBlog.com and winner of our Machining Metal as a Hobby contest.
The Craftsman 15″ Drill Press, Model 137.229150, is a floor model commonly found in many home shops. Made by Rexon of Taiwan for Sears, Grizzly and others it is a typical consumer grade drill press. When new this machine is quite functional and if you use it to drill holes in wood and the occasional piece of metal then this drill press will give you years of service. However, if you are a metal worker and need more accuracy in your machine it’s a whole other ball game.
The accuracy of these machines when new is not too bad but in a few short years mine developed significant run out, with 0.003″ total indicator run out (TIR) at the spindle and double that at the chuck. That may not seem too bad but let me tell you, 0.006″ of run out at the chuck is enough to visibly see the bit wobbling! My spindle bearings had developed play that I could hear and feel and I knew it was time to do something about it.
While it may appear to be daunting it turns out that restoring it is not difficult. However, it does require access to a hydraulic press and a puller for the spindle pulley so take that into consideration. Other than these tools no special tooling is required beyond that found in the typical home shop. If you or your friends don’t own a hydraulic press all machine shops and most auto repair shops do; the cost to press the bearings off and on should be minimal.
If we consider where run out could come from it will likely be the spindle assembly, the arbor or the chuck. The spindle assembly is basically the drive sleeve that drives, supports and guides the spindle at the top, the solid spindle itself, and the four bearings that support these components. I suppose the quill could contribute but unfortunately there is no provision for improving the accuracy of the quill so it’s a moot point.
The manual does not list part numbers for the above components but you can order them from the Sears Parts Direct website at reasonable cost using their illustrated parts breakdown. I suggest replacing the spindle, the drive sleeve and all four bearings at this time.
I also suggest you obtain precision after market bearings instead of using the OEM bearings. You will need 3 each 6204ZZ and 1 each 6203ZZ. I chose to replace one of the 6204ZZ bearings with a 6204-2RS; this bearing is sealed and resides at the bottom of the quill where it is exposed to chips and cutting fluid. All of these bearings are available from your local supplier but are cheaper on eBay. I prefer to use Nachi bearings for their quality but this is a personal choice.
If/when I need to rebuild my drill press again I will use an angular contact bearing to replace the lower quill bearing; the near equivalent for the 6204-2RS is the slightly longer 5204-2RS. Note that I have NOT done this yet so I’m not sure if the bearing would protrude a few millimeters. If it did you could chuck the quill in the lathe and bore the bearing recess deeper, or live with a little protrusion. Only the lower bearing needs to be an angular contact bearing; radial bearings are fine for the upper spindle bearing and drive sleeve. Why an angular contact bearing?
Angular contact bearings are designed to take both axial and radial loads, unlike radial bearings which are made for radial loads only. Consider that when using a drill press to push a drill into a work piece both axial and radial forces are at work. Sort of makes you wonder what the designer was thinking, doesn’t it? Take a look at a good American drill press, like a Clausing, and you’ll find an angular contact bearing at the end of the spindle.
The chuck arbor is another potential source of run out and I typically change it to a new Albrecht or Jacobs arbor when installing a new chuck. The OEM spindle requires a #2 Morse Taper.
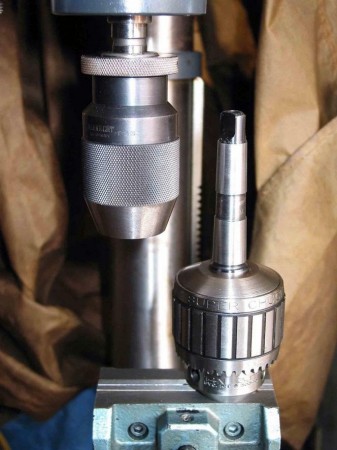
If you are using the OEM chuck for woodworking or general use then it may suffice. However, I would consider replacing it if you need to drill a precision hole. You can use a keyed chuck, like the Jacobs Super-Chuck 14N on the right, or a keyless chuck like the very accurate Albrecht on the left. Both are far more accurate than your drill press will ever be and can be had on eBay at reasonable cost. If I could only have one chuck I would choose the Albrecht for the obvious convenience and accuracy it provides.
In summary, we are going to replace the parts in the drive train that could be causing run out and consider replacing the arbor and chuck, which are additional sources of potential run out.
Okay, let’s get this thing apart! As always, please work carefully and proceed at your own risk.
Teardown
- Use your arbor wedge to knock out the arbor and chuck. If you don’t have one you can make one from 1/8″ thick mild steel.
- Remove the light bulb from its socket.
- Loosen the two set screws that hold the head to the column and move the head to your work bench. It is heavy so try to have another person assist you if possible.
- Open the belt cover and remove the belts. Now remove the nut at the top of the spindle – this is a LH thread. You can insert the arbor wedge into the slot in the quill to hold the spindle still.
- Remove the spindle pulley. You will need a pulley puller for this.
Remove the quill.
- Loosen the quill adjusting set screw just to the right of the spring.
- On the left side of the head find the quill return spring assembly. It has two nuts; the outer one is a jam nut. Remove the jam nut.
- The manual recommends that you place a screwdriver into one of the slots to control the spring as you release tension but I just used a gloved hand to grab hold of the spring housing and, while controlling the spring tension (turn the housing slightly CCW), remove the nut. The tension is not that strong and is released in about a single turn. It will look like this when removed [photo 4].
- Turn the feed handle and catch the quill as it drops out.
- You can now disassemble the quill. There is a piece of plastic tubing on top of the assembly which looks suspiciously like a Taiwanese anti-grease slinger device. Under that is the spindle nut, a nut lock washer and a flat washer – in that order.
- The Nut Lock will have one of the ears bent up to keep the Spindle Nut from turning; using a punch, carefully bend it down so the nut can be removed.
- Now remove the spindle nut (RH thread). Note: the tension on this nut is minimal. It is run down to contact the bearing and turned until one of the tabs on the nut lock can engage a slot. Typically, this arrangement is used to preload a bearing but in this case I think it just keeps the bearing from being displaced.
- Now remove the nut lock and flat washer and set them aside.
- Here is where you will need your hydraulic press. Drive the spindle out of the quill from the top. Once the spindle is out you can tap the bearings out of the quill with a brass punch or hardwood dowel. You will notice the two bearings inside the quill differ; the upper one is smaller – the 6203ZZ – while the lower one is the 6204ZZ. This lower bearing is the same as the paired bearings on the drive sleeve. [Photo 6]
Remove the drive sleeve from the head.
- The drive sleeve [photo 7] is held in place at the top of the drill press head by two “Circlips”, one on top and one underneath the Drive Sleeve. Remove the upper clip by grasping one ear of the clip and slipping a slim screwdriver behind the clip. Carefully work the clip out. The one under the drive sleeve can be left in place.
- Use a hardwood dowel and tap the drive sleeve assembly [photo 8] out from below – that is, stick the dowel into the head from the bottom side and use a dead blow hammer to tap the drive sleeve out toward the top. It is a loose press fit but tap evenly so you don’t cock it as you drive it out.
- Now press the drive sleeve out of the two bearings. Note that you need to position the unit with the threaded part down. Support the bearings and then use a piece of stock smaller than the inner bearing race that bears on the center column of the sleeve so it can be pressed out. The two bearings are separated by a plastic ring that you need to retrieve even if you are replacing the drive sleeve and bearings.
[table id=3 /]
Disassembly is now complete and all parts can be cleaned and inspected.
Assembly is basically the above procedure in reverse.
Use grease sparingly during assembly. You need to grease the spindle but remember that the spindle is moving up and down through the drive sleeve during operation and the belts are subject to flying gobs of grease as this occurs.
- Press the drive sleeve into the two drive sleeve bearings with the plastic ring between them.
- Clean the socket that will receive the drive sleeve.
- Install the drive sleeve assembly into the head. Put a light coat of oil on the outer bearing race of the drive sleeve bearings and push the drive sleeve assembly into place from the top. Try pushing it into place manually; if the bearings align correctly you can push or gently tap the assembly into position. If it won’t go in easily then you can pull it into place using a threaded rod passed through the assembly. Use a scrap of wood or metal below and a washer and nut on top and tighten the nut to pull the assembly down. You only need to get it in far enough to install the upper circlip. Do not distort or damage the lower circlip.
- Install the quill.
- Assemble the quill and spindle with their bearings.
- At the top of the spindle, install the flat washer, the nut lock, and then the spindle nut. Snug the spindle nut then back it off to engage the nearest tab on the nut lock that will engage and bend that up.
- Re-install the plastic tubing. Clean the quill itself, with attention to the teeth on its side and apply a light coat of oil.
- Insert the quill into the head and engage the handle to crank the quill up.
- Install the quill return spring assembly – essentially the reverse of the above. Remember to preload the spring about one turn before locking the nut down. Install the jam nut.
- Re-install the pulley and belts and re-install the head onto the column. Adjust the quill set screw to minimize play but be sure the quill moves freely.
- Re-install the light bulb.
- Install your arbor and chuck and you are … Done!
I would recommend doing a rebuild if you are having run out issues. It’s not hard to do and the cost is more than acceptable (if you don’t count a new chuck). The improvement in performance is significant – run out at the arbor on my drill press is now less than 0.0005″ TIR and that drill bit looks like it’s standing still!
Mikey
2006
Update: It is now February 2010 and the run out at my arbor is still under 0.0005″ TIR despite hard use in a typical hobby machine shop. I believe the use of high quality bearings minimizes wear on the spindle and drive sleeve and help to maintain accuracy. At this rate I may never get to try that angular contact bearing!
It appears that many of the photos from this article have disappeared – anyone have them?
Sent you a PM, Jay.
Mikey
The missing pictures have been restored. They disappeared because of the problems we had with hackers last weekend. Please let me know if you notice any more problems. I still haven’t quite finished reinstalling or reconfiguring some of the plug-ins I had to delete. – Rob
I sent a pdf of the original article to Jay so he could get on with his drill press restoration, Rob. I am sorry to hear about those hackers and the problems they are causing.
Mikey
Great article. I am thinking I need to do this to my Craftsman. I have a couple of questions. I have a 17″ (113.21317). I am assuming that the process is nearly identical to what you describe here? What about the bearings? Are they very different? How do I find them for my model?
Also, before I get into this, how can I be sure that I need to replace the bearings? Right now I have about a 1/8″ (.018″ or so with the dial indicator) of play in the entire quill. I can wiggle the entire assembly with my hand. The quill adjustment screw doesn’t seem to get me very much difference. I had had this DP in my garage for almost a year while I was renovating my shop. When I put it all back together and began to clean and tune all the machines, I noticed that the DP now had a ton of play. It is possible that I just didn’t realize how bad it was or became from the time of my purchase. I had bought it only a year prior to putting it in the garage, so I can’t be sure that the play wasn’t already getting that bad. But is it possible that something else could be the culprit that I am missing? How can I check, without having to take the whole thing apart? Or should I just take the whole thing apart anyway on the assumption that I will not otherwise be able to reduce the runout to acceptable levels?
Thanks for your advice.
Hi ???,
The decision as to whether or not to rebuild a drill press depends on the runout at the spindle, not the quill. If you are getting 0.018″ RO at the quill (or is it really ten times that at 1/8″?) then you need to adjust the play in the quill. The quill adjustment screw should be able to take up 0.018″ easily; just loosen the nut and turn the slotted adjuster in a ways. Be sure you are working on the quill adjustment screw, which is just in front of the quill return spring. It is very unlikely that the drill press developed excessive play just from general use while rebuilding your shop. However, these machines are loose from the factory and you just need to adjust the quill adjustment to take up the slop.
If your quill adjustment screw doesn’t help then either it is hung up on a burr or there is some problem with too deep a quill slot, in which case a longer screw should fix it. Try taking the screw out and have a look in there; the screw just bears on the bottom of the slot so make sure it is doing just that.
If you are able to tighten up the quill and still have unacceptable RO then it is time to replace the bearings, in which case you will need to disassemble the drill press. This is the only reason I would tear down a drill press – unacceptable play in the SPINDLE. By unacceptable, I mean whatever RO you think is excessive. For general shop use, a RO of 0.005″ may be fine. For a metalworker, 0.001″ would be acceptable. It really depends on what you need.
I have not rebuilt a 17″ press so am not sure if it is the same but suspect it is very similar. Your OEM bearings will be stamped with the number of the bearing somewhere on the side of the bearing; just replace it with the same numbered bearing and you should be fine. I would suggest a sealed bearing for the lowest bearing at the bottom of the quill, or better yet – an angular contact bearing.
Let me know how it goes.
Mikey
Mikey,
Thanks for the quick reply. I can’t seem to get the sort of adjustment out of the quill adjustment screw that I think I should be able to, but part of the issue is how to make the measurements, I think.
I removed the adjustment screw and found that it is slotted to fit into the slot of the quill. This prevents it from turning 360. SO, I filed off the sides of the slot at the end of the screw making it round. I hope that’s not a bad idea, but it seemed like a good start toward understanding the problem. Anyway, now I can tighten the screw all the way until I can actually lock the quill in place. Doing this, and with the quill completely extended, I still get about .009 runout. Here’s a questions though. Should I measure runout with the DP running or should I turn the chuck and spindle by hand? When I turn it by hand slowly and carefully I get about .007 runout. The other question is that I can push on the quill and physically deflect it about .018. The entire assembly can be pushed in any direction this amount. Should I be worried about this or is this irrelevant to the operation?
I can’t understand really how this amount of play in the quill could be worked with, but also how replacing the bearings is going to fix it. Is this just a poorly made DP or am I missing something here?
Thanks again for your help. Sure makes my life easier!
Mike
Hi Mike.
Given the way we normally drill an accurate hole, a little play in the quill itself isn’t too important. I just adjust the quill adjusting screw until I get free motion of the quill up and down, but only just. If you tighten that quill adjustment screw until it just allows free movement then that is the best we can do, unfortunately.
There are only three ways to drill a hole with the press:
1. Eyeball it.
2. Center-punch the mark and use the punch to guide the drill.
3. Scribe a center with cross marks and try to drill at the intersection with a center or spotting drill and follow up with our twist drills.
In all of these situations the play in the quill won’t materially alter our accuracy … but runout at the spindle, arbor or chuck will. I’m sure you realize that once the drill begins cutting the quill is not going to be moving around much, and in fact a little play in the quill is necessary to allow the spindle to center itself. What really matters is the RO at the spindle and the arbor/chuck assembly. In my experience, the bearings are usually the source of greatest RO, followed by the drive sleeve, followed by the spindle itself. This makes sense if you think about what components are subject to the most wear over time.
I typically measure RO with my spindle turning at low speed, maybe 350 RPM, with belts tight. I know there are some guys who turn the upper pulley (belts off the pulleys) by hand and gauge RO that way but it makes more sense to me to have a dynamic reading at speed. I use a dial test indicator and zero it to the spindle, turn on the press, and read both the spindle, then the arbor. Recall that the reading you get will be the Total Indicator Runout (TIR), and that the true RO is about half this amount. The small amount of side loading from the DTI won’t materially affect your accuracy.
I check RO with the quill fully retracted and also fully extended to see what the difference will be. If your bearings and spindle are in good shape there will be very small differences in the RO readings. This does assume the quill is machined accurately but on a Taiwanese drill press it is usually fairly good. Can’t say the same for Chinese products.
The Rexon presses are consumer grade machines and will actually drill pretty accurate holes. I have used a really nice Clausing drill press and while it is far better in both design and construction it was not any more accurate than my rebuilt Craftsman. In both cases I put the hole exactly where I wanted it. The one area where an industrial press is superior is in the stroke of the quill. For a Clausing or a 20″ Jet press you get about 5″ of stroke on the quill; with a Craftsman you get only about 3.5″. This makes drilling larger holes harder because you can’t get a large jobber drill chucked up without moving the table and thereby destroying your accuracy. I use screw machine drills to get around this problem but it is a pain that I intend to remedy one day (if I ever find a used Clausing for a decent price).
Sorry to ramble. So … just adjust the quill to minimize play. Read the RO at the spindle with the machine on and with the quill retracted and then fully extended. Decide if the RO is acceptable or not, then decide if a rebuild is needed based on your degree of RO tolerance.
Mikey
Thanks a So much you sure saved me a lot of time and research.
You’re welcome, Phil. Let me know if there are any problems.
Mikey
I have the Craftsman 137.229150 press. I would like to know if you know the quill dia. I am trying to purchase a mortise att. from Delta and I need to know the dia. Any help would be appreciated, thanks Nick
Hi Nick, mine is 47mm OD. It looks like the Delta Mortising Attachment should fit – they list a 48mm adapter, which should work.
Mikey
Thanks for the quick reply Mike that was a big help. I’m interested in refurbing my drill press as well. What you have done to yours is great. It would have never crossed my mind. Thanks and Happy New Year.
Go for it, Nick. Its pretty easy to do and the results are worth it. If you need any help please let us know. Happy New Year to you as well.
Mikey
Mikey
Thanks so much for your informative article on tuning & tightening the quill of a drill press. I have a KTF brand machine made in Taiwan. Its always had a loose quill .015″ play which has been annoying for the past 35 yrs or so since I purchase it new.
Made the adjustment today & now have .005″ movement with a .005″ max runout.
All fixed thanka again
Bruce Smith
Dural NSW Australia
(Down Under)
You are most welcome, Bruce. Glad to know it helped.
Mikey
I have a craftsman 2/3 HP 13 inch variable speed drill press, model 137.229130. After a little accident with a hole saw it seems that there is significant runout. Basically the hole saw bit was mangled by the time I shut off the power as it caught on the drill vise.
I’m not sure what is causing the runout, if I remove the arbor/chuck, I don’t see anything visible at the spindle, when I put the arbor/chuck back in, and put in a longer drill bit, there is a little visible runout. I am thinking the quick solution is to get at new arbor and chuck and see if that corrects the problem. I’m not sure if I want to invest in the time or energy to go throughout the overhaul as you’ve instructed.
I can get the parts new on the Sears parts website totaling $97 plus shipping, or I can get a used Albrecht 1/32″-1/2″ Keyless Drill chuck No.2 morse taper (made in Germany) on ebay for around $50. Do you have any advice for me, is it worth a shot to get the Albrecht which seems to come with the arbor? Thanks for any advice.
Hi Keith,
It seems unlikely to me that you damaged the spindle/quill assembly just from this little incident so I agree that an overhaul is probably not necessary just for this. If I had to guess I would think the chuck arbor got knocked out of alignment or may be bent. Before buying something I would take the existing arbor out of the chuck and put it in some V-blocks and check it for straightness. If its straight then see if reinstalling it corrects the problem. If its bent then buy a new arbor – I suggest a Jacobs arbor to keep costs low. The chuck is not likely to be bent so replacing it shouldn’t be necessary unless you want a better chuck anyway.
I would not replace the arbor with an OEM Sears part. I would buy a Jacobs or Albrecht arbor instead.
If you want a better chuck then a used Albrecht would be a good idea. I do not like chucks with integral tapers, simply because if anything damages the arbor then I’m screwed. Luckily, most MT2 Albrecht chucks have replaceable arbors and that is the type I would buy. You might also consider a Rohm Supra keyless chuck; these are quite good at half the cost of an Albrecht. If you do a lot of heavy drilling with large bits or hole saws then a Jacobs Super-Chuck is a good choice because you can lock that sucker down tight and it will not slip.
I hope this helps. If not, please let me know.
Mikey
Mikey
Thanks so much for the quick and amazingly helpful reply.
I just took out the arbor (which was basically falling out on it’s own) and followed some other advise for cleaning it and the spindle hole, putting some talcum on it and reinstalling it. I haven’t yet tested it to see if the runout is better. I didn’t check the straightness but I probably should before going much further. The used Albrecht I’m looking at is here:
http://www.ebay.com/itm/Albrecht-1-32-1-2-Keyless-Drill-chuck-No-2-morse-taper-made-Germany-/190636548480?pt=BI_Tool_Work_Holding&hash=item2c62d2e180#ht_500wt_1413
or here:
http://www.ebay.com/itm/JACOBS-ALBRECHT-TYPE-KEYLESS-CHUCK-2-MORSE-TAPER-1-16-1-2-PORTOMATIC-/300660144647?pt=BI_Tool_Work_Holding&hash=item4600bdba07#ht_500wt_1413
It looks like both have the arbor attached, do you think either of these is worth getting? Seems like it’s a direct replacement for my Sears arbor and chuck. (the replacement arbor part on the Sears site is here: http://www.searspartsdirect.com/partsdirect/part-number/21015M2J30/0009/137&blt=04
Again, thanks.
-Keith
Hi Keith,
I would not go for either of those chucks. The Albrecht does not have a collar so getting the chuck tightened might be a problem. The Jacobs chuck is not a common model so not sure about replacement parts. You are looking for a Albrecht model J130, a 0-1/2″ chuck with a removable arbor. To my knowledge this model comes with a Jacobs 33 taper so you can buy a good arbor with a Jacobs 33 taper on one end and a MT2 taper on the other.
Here is an example of such a chuck: http://www.ebay.com/itm/Keyless-Albrecht-Drill-Chuck-Mod-130-J33-1-32-1-2-MadeInGermany-lathe-mill-/250990917847?pt=BI_Tool_Work_Holding&hash=item3a703978d7
I agree – check your arbor first. If its bent then get a new arbor and use your old chuck if it is accurate enough for you. I would personally buy a used Albrecht and recondition it, then buy a good new arbor and be good to go.
Let me know if there is anything else.
Mikey
Mikey,
Great article and info above. I may have found the answer man for my problem. I have an older Craftsman DP, made by King-Seely I think. It’s from the 50’s as best as I can tell. The ID tag is missing. I’ve bought it used and have used it for years doing metal work. I haven’t used it that hard really but, the PO may have. My quill play seems excessive to me (uneducated in this type of thing). My next project will be spot facing 12 holes and I am concerned about this quill play. I don’t have a mag base yet for my indicator so I can’t really measure the play. Will this play result in a poor job? There is no simple fix for this problem that I have found so, I am considering just buying a different press in better condition. Also, I can see no set screw, as in the diagrams, to remove the belt pulley. There is a small hole the is drilled at an angle to the spindle that goes through the pulley from the top. It’s very small, like an oiling hole rather than a set screw. Do I need a puller to remove the pulley and begin disassembly of the machine?
Hi Mikey, collecting the parts for my rebuild project and I was wondering if an 18N (3/4″)or a 5/8″ chuck would work in place of the 14N. What do you think?
Mikey; Great article – wonderfully clear and well written. My old but low mileage Sears 113.213151 15″ 1HP drill press with a Rohm J3S3 chuck/taper has pretty decent TIR of .002″, good for my mostly woodworking and occasional metalworking projects. I take this to mean the bearings/spindle/drive sleeve are fine. However the quill is quite loose. When fully extended the quill can be manually rocked forwards .025″. When retracted it rocks forward .01″. The quill does not rock back or side to side, only forward. I’ve snugged up the quill adjustment screw as tight as I can while still getting free quill movement. 99% of the time I am OK with this quill movement. Sometimes it is hard to get accurate holes started in wood – say doing a series of Forstner bit cuts to make a deep mortise and so I’d like to limit my quill slop. One thought is to buy a new Tube Quill. Sears no longer makes the spindle or the head so the $32 quill is my only option. What would you suggest? Seems the head is more likely to be over-bored then the tube quill under-sized. Maybe bore, tap and run set screws thru the head to push the quill back?? Any help would be much appreciated. Or is it time to buy a new drill press?
Thanks – Millo
Hi Dave,
I apologize for the late answer – I was busy fixing my son’s car for a few days and only now am getting to my email.
I have no experience with the older King-Seeley/Sears DP but understand they were quite good. I assume you have the manual that is available from this site: http://vintagemachinery.org/pubs/detail.aspx?id=4890. It shows a set screw that locks the pulley to the pulley insert and it should be there. If you can find it that pulley should come off, though I am not sure if a puller is needed. There are a number of online discussions re this DP and you should be able to find them easily.
It also looks like the quill play can be adjusted with a cap screw and I would try that. All DP will have some play at the quill and typically this isn’t a problem. In fact, I think it allows the drill to center more easily so some play is a good thing, provided you have a center punch mark or have center-drilled to get things started.
As for spotfacing, how well this works depends on which type of tool you are using. If you try it with an end mill on a DP it will not go well; the play in the quill will not provide enough rigidity. If you must face the surface on a DP then a piloted counterbore would be your best bet. I do this all the time and it works well. Just be sure to keep your speed low, use lots of lube and a positive feed.
Sorry I’m not much help here. Let me know if there is anything else I can help you with.
Mikey
Hey Nick,
As long as you can find an arbor to fit the chuck to your press either chuck should be fine as long as you don’t need to hold really small drills.
Hi Milo,
Thanks for the kind words.
Most of these Sears drill presses have a simple screw that runs in a slot on the side of the quill to adjust the quill play. If you have excessive forward play then it may be possible that the adjustment screw is just worn. Have you checked the screw? If it is worn then you can easily make or purchase a new one that will fit the slot. If the slot itself is worn then you may be able to mill the slot sides straight and fit a spacer around the quill screw and minimize play that way. If you don’t have a mill a machine shop should be able to do it pretty easily or you can buy a new quill.
It isn’t time for a new drill press, Milo, unless you stumble upon a used Clausing for cheap. That old Sears press will serve you well in a wood shop for many years with just a little love.
Let me know if this helps, or not.
Mikey
Chances are, the end of the adjuster is worn. I don’t think it’s hardened. I’d turn it down to a nominal drill size, and make a small square key to fit the quill slot. Drill it to fit the end of the adjuster, and you’ll have a more positive fit all around. Essentially, you’re making an adjustable gib.
Proper adjustment is critical. Tighten down the adjuster screw to fairly snug. The quill should be very tight at this point. Back off the adjuster about 1/8 to 1/4 turn. Holding it from turning, tighen down the locknut. This should give you freedom of vertical movement in the quill, but not let it move front to back. Make sure things are properly lubricated, or you’ll end up adjusting it again in the future.
Mikey – A small square key to fit the quill slot is a wonderfully clean and simple solution. Most excellent idea! Looking at the old adjuster it does not look worn except on one corner. It does beg the question (posed by Mike on July 21,2011) that since the sides of end of the adjuster are ground away into a Mohawk (looks like an inverse flathead screw) and the length of the Mohawk is wider that the width of the quill slot there is no way the screw can be driven down into the slot to snug everything up. As a quick test I can grind the “Mohawk” down to a “post” like Mike did and snug it down into the slot. While temporary (the sides of the post will wear over time) that will prove the concept and then I can, at my leisure, make the post even smaller and fabricate a square “cap” for it. If I find an old drill bit that exactly fills the slot I might bore a hole in the adjuster, cut off the end of the drill bit to make a short rod, and replace the rod whenever it gets worn. Thanks for the expert suggestions.
Millo
Hello Mikey,
Success! Rounding the tip of the adjuster and running it in until the quill just barely returns yields NO slop when fully retracted. When fully extended the slop is reduced from the previous .025″ to .020″ slop. My thinking is that fully extended slop is a don’t care, what matters is how controlled the bit is when it initially hits the drilling surface. From then on it tends to follow the hole it started. Now that the concept is proved I’ll pursue either the square cap or piece of old drill bit solution.
I do wonder how the original adjuster screw could ever work given it is too big to set down inside the slot on the quill. Is this a mgf defect? Seems like the adjuster screw should end in a post whose diameter fits just inside the quill slot. Thanks again – Millo
Okay. I guess I didn’t realize that the quill lock can be used to adjust the play in the quill as well as to lock it in position. I’ve used it this way but thought I was doing something I shouldn’t do and possibly damaging the machine. As for the spot facing operation, a piloted counter bore is what the plan is. Thanks for reassuring me on this as the best way to do it.
For the life of me, I can’t find that set screw. I’ve looked several times. But, perhaps it’s a non-issue for now, ehh?
Thanks again.
Oh, what rpm would you suggest for the spot facing? The work piece is cast steel. I think I am already as slow as it’ll go.
Millo, I’m glad you got it worked out. Rleete’s suggestion is a good one and I would try a spacer that is shaped to fit the slot, too.
Dave, I suggest countersinking at the lowest speed your DP will go. There will be a lot of cutting surface in contact with the work so the probability for chatter is pretty high. Going slow will help minimize that. A good fit of the pilot in the hole is important in minimizing chatter, as well. I haven’t countersunk into cast steel before but in all materials I have done it in I try to feed slowly until I get an initial flat surface, and then I increase the feed force to keep the tool cutting continuously. Done this way it cuts fast and clean without chatter. Use a good lubricant and you should be good to go.
Not sure what to tell you about that set screw. It should be there but if it isn’t then that pulley is pressed on and you may need to press it off.
Mikey
After all that futzing around I still have slop in the extended quill of my Sears DP so went off and found (thank you Craig’sList!!) a lightly used Dayton 3z568 15″ variable speed DP for $180. It is “Made in the USA” so the tolerances are super and parts are available as it is functionally equivalent to a Wilton A5816/Jet J-A3816. Mine has no crank on the table, you just muscle it up or down, and a mechanical speed indicator (400 to 5000 RPM) instead of the newer LED one but other than that is dead accurate with .001 TIP when the quill is extended the full 6 inches. Not quite a Clausing but pretty close and nowhere near as pricey…. The motor is not aligned so have to enlarge some holes and the drive pully does not snug down on the shaft but once I work through those it should be good to go.
Guess I’ll be selling my old Sears 113.213151 DP
Nice score, Millo! If I recall, those have a 5″ or 6″ travel on the quill – now I have DP envy!
Does anyone know the belt sizes (2 of them) for a Mastercraft 15 inch floor model Drill Press Model -55-5916-2
Have checked with Mastercraft They dont even know
Thanks would certainly appreciate the info
Joe, I’m not sure but I looked at pictures of the Mastercraft drill presses and they look like they were made by Rexon. The main casting, the switch housing, even the belt covers look the same. I would guess the belts to be the same as mine BUT I am guessing at this. Canadian Tire does not list manuals for their machines but Sears Direct has parts for good prices.
If you go here: http://www.searspartsdirect.com/partsdirect/part-model/Craftsman-Parts/Drill-Parts/Model-137.229150/0247/0713080/10059827/00001
… and look at parts 86 and 93 in the drawings you will find the belts that are common on all the Sears 15″ presses. These belts last for years and for under $10.00 it would be worth a try.
Hope it works out.
Mikey
Hi Mikey,
I’m in the middle of a similar rebuild, and feel lucky to have found your website! Thanks for the great article.
I have a question related to the angular contact bearing for the bottom quill bearing. Is there any reason a 7204-2RS would not work? It is the same size as the 6204-2RS.
Thanks,
MB
Hey Mike,
I haven’t any experience with ceramic bearings but understand they are a great many advantages to them. If you go with one please let us know how it works. I still haven’t found the need to change mine but just might if your report is favorable.
Oh, and yes, as long as the bearing dimensions are the same as the 6204-2RS then it should fit.
Mikey
I have an old 15″ Craftsman and all of a sudden the quill will not go up or down. Any idea what might be causing that problem?
Thanks,
Mike C.
Hey Mike,
Sorry to hear you’re having problems. The quill mechanism is pretty simple: just a drive shaft with gear teeth that engage threads on the quill; this is called the feed shaft. If the gear teeth are stripped then replacing the feed shaft should fix it. It is unlikely that the spindle adjustment is so loose that the gear won’t engage but you can try loosening the lock nut on the quill adjuster and tighten it to see if that helps. However, if I had to guess I would suspect the feed shaft has stripped out and needs to be replaced.
Sears sells the replacement parts for pretty low cost. Check Sears Parts Direct and type in your model number to find the right part.
Mikey
Sounds to me like the gear that engages the rack on the spindle is stripped out. I’ts probably either keyed or pinned. If that’s the problem, it should be a fairly simple fix, the hardest part being tearing it all down.
My arbor fell out of my 15″ craftsman drillpress model 137.229150. Is it just a press fit to put it back?
Sorry it was my chuck that fell out.
Hi Coop,
Take a look at the following link and see if this solves your problem. If not, then let me know. It’s likely the taper of the chuck or arbor is dirty or has a burr on it.
https://www.machinistblog.com/installing-a-drill-press-chuck/
Mikey
Hello Mickey,
I have the same drill DP3800FL from Rexon.
I have at least a mil play between the spindle and drive sleave grear. Here I was told they are selling only the complete assembly? Does Sears sell the drive sleave only without bearings and the spingle itself.
Do you have some part numbers for me?
BR
Robert
You can find it on this page:http://www.searspartsdirect.com/partsdirect/part-model/Craftsman-Parts/Drill-Parts/Model-137229150/0247/0713080/10059827/00001?blt=06&prst=&shdMod=
They sell just the drive sleeve:PART NUMBER: 10606505
The spindle is: PART NUMBER: 10605822
Hope that helps,
Mikey
The Rexon part are 05YN & 05YC. I only have the rexon part no in my service manual.
Here in Germany they are selling you the whole assembly and not the siggle part.
Thank You.
Do you know if there if the Driving Spindle is tempered?
Is some clearance between spindle and drining Sleeve Std.
May I send you some picture to rate my clearance?
BR
Bob
Hi Bob,
I do not know if the spindle is tempered but I am guessing it is not. A hardened part may snap under load.
Yes, there will be some clearance between the spindle and drive sleeve, and 1mm doesn’t seem to be excessive.
It may help if you tell us what the problem is with your drill press.
Mikey
Hi Mikey,
It was starting loud banging when I was grinding with it.
So I took it apart and Like to improve it.
I am going to replace the bearings. One of them looks bad to me.
Se my video of the spindle clearance. Why shall it be so hight. Is my spindle busshing worn. I see some little chips but it that normal?
http://www.youtube.com/watch?v=aVpdbL-A_cY&feature=youtu.be
Bob, I can’t recall how tight the fit is on a new sleeve and spindle but I don’t think its too much tighter than what your video shows. Once the motor starts the play in the drive sleeve is taken up so I don’t think that is the cause of your banging sound.
I would suspect the bearings are gone, and if I had to guess which one then I would suspect the lowest one. These bearings are not meant to take lateral force, like grinding. I suggest replacing ALL four bearings and see how it goes. eBay should have what you need. If you still have the banging issue then the only thing left would be to replace the drive sleeve and spindle.
If you look at the June 4th comment by Mike B, he used a ceramic angular contact bearing for his lower quill bearing. I think this is an excellent idea that I will be emulating the next time my press is apart. I don’t know how it worked out for him but I personally would opt for his bearing choice for the bottom quill bearing. I don’t know if Mike B. is on this site very often but you might try asking the blog administrator for his email address to see how it all worked out.
Let us know how it goes, Bob.
Mikey
Mickey & all other readers,
may you check on your drill press about the clearance
of spindle to spindle drive.
Mikey the JET replacement cost double as the craftsman part.
the must be some differences? Same part no!!!
Very easy. Open your belt cover on top. You will see the
belt pulley and the tip of the spindle. Hold the pulley and
move the spindle. Tell me what do you observe.
Bob, I can’t recall how tight the fit is on a new sleeve and spindle but I don’t think its too much tighter than what your video shows