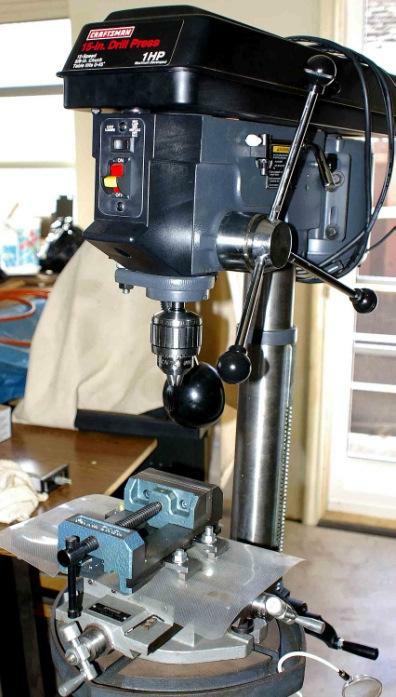
This is another excellent article by Mikey, a frequent contributor to MachinistBlog.com and winner of our Machining Metal as a Hobby contest.
The Craftsman 15″ Drill Press, Model 137.229150, is a floor model commonly found in many home shops. Made by Rexon of Taiwan for Sears, Grizzly and others it is a typical consumer grade drill press. When new this machine is quite functional and if you use it to drill holes in wood and the occasional piece of metal then this drill press will give you years of service. However, if you are a metal worker and need more accuracy in your machine it’s a whole other ball game.
The accuracy of these machines when new is not too bad but in a few short years mine developed significant run out, with 0.003″ total indicator run out (TIR) at the spindle and double that at the chuck. That may not seem too bad but let me tell you, 0.006″ of run out at the chuck is enough to visibly see the bit wobbling! My spindle bearings had developed play that I could hear and feel and I knew it was time to do something about it.
While it may appear to be daunting it turns out that restoring it is not difficult. However, it does require access to a hydraulic press and a puller for the spindle pulley so take that into consideration. Other than these tools no special tooling is required beyond that found in the typical home shop. If you or your friends don’t own a hydraulic press all machine shops and most auto repair shops do; the cost to press the bearings off and on should be minimal.
If we consider where run out could come from it will likely be the spindle assembly, the arbor or the chuck. The spindle assembly is basically the drive sleeve that drives, supports and guides the spindle at the top, the solid spindle itself, and the four bearings that support these components. I suppose the quill could contribute but unfortunately there is no provision for improving the accuracy of the quill so it’s a moot point.
The manual does not list part numbers for the above components but you can order them from the Sears Parts Direct website at reasonable cost using their illustrated parts breakdown. I suggest replacing the spindle, the drive sleeve and all four bearings at this time.
I also suggest you obtain precision after market bearings instead of using the OEM bearings. You will need 3 each 6204ZZ and 1 each 6203ZZ. I chose to replace one of the 6204ZZ bearings with a 6204-2RS; this bearing is sealed and resides at the bottom of the quill where it is exposed to chips and cutting fluid. All of these bearings are available from your local supplier but are cheaper on eBay. I prefer to use Nachi bearings for their quality but this is a personal choice.
If/when I need to rebuild my drill press again I will use an angular contact bearing to replace the lower quill bearing; the near equivalent for the 6204-2RS is the slightly longer 5204-2RS. Note that I have NOT done this yet so I’m not sure if the bearing would protrude a few millimeters. If it did you could chuck the quill in the lathe and bore the bearing recess deeper, or live with a little protrusion. Only the lower bearing needs to be an angular contact bearing; radial bearings are fine for the upper spindle bearing and drive sleeve. Why an angular contact bearing?
Angular contact bearings are designed to take both axial and radial loads, unlike radial bearings which are made for radial loads only. Consider that when using a drill press to push a drill into a work piece both axial and radial forces are at work. Sort of makes you wonder what the designer was thinking, doesn’t it? Take a look at a good American drill press, like a Clausing, and you’ll find an angular contact bearing at the end of the spindle.
The chuck arbor is another potential source of run out and I typically change it to a new Albrecht or Jacobs arbor when installing a new chuck. The OEM spindle requires a #2 Morse Taper.
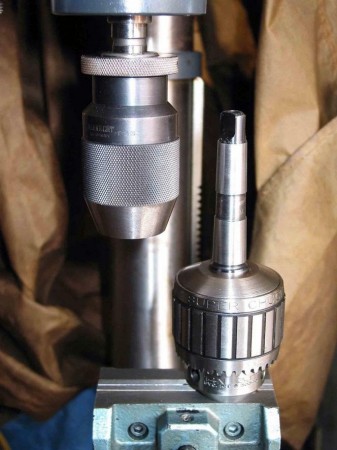
If you are using the OEM chuck for woodworking or general use then it may suffice. However, I would consider replacing it if you need to drill a precision hole. You can use a keyed chuck, like the Jacobs Super-Chuck 14N on the right, or a keyless chuck like the very accurate Albrecht on the left. Both are far more accurate than your drill press will ever be and can be had on eBay at reasonable cost. If I could only have one chuck I would choose the Albrecht for the obvious convenience and accuracy it provides.
In summary, we are going to replace the parts in the drive train that could be causing run out and consider replacing the arbor and chuck, which are additional sources of potential run out.
Okay, let’s get this thing apart! As always, please work carefully and proceed at your own risk.
Teardown
- Use your arbor wedge to knock out the arbor and chuck. If you don’t have one you can make one from 1/8″ thick mild steel.
- Remove the light bulb from its socket.
- Loosen the two set screws that hold the head to the column and move the head to your work bench. It is heavy so try to have another person assist you if possible.
- Open the belt cover and remove the belts. Now remove the nut at the top of the spindle – this is a LH thread. You can insert the arbor wedge into the slot in the quill to hold the spindle still.
- Remove the spindle pulley. You will need a pulley puller for this.
Remove the quill.
- Loosen the quill adjusting set screw just to the right of the spring.
- On the left side of the head find the quill return spring assembly. It has two nuts; the outer one is a jam nut. Remove the jam nut.
- The manual recommends that you place a screwdriver into one of the slots to control the spring as you release tension but I just used a gloved hand to grab hold of the spring housing and, while controlling the spring tension (turn the housing slightly CCW), remove the nut. The tension is not that strong and is released in about a single turn. It will look like this when removed [photo 4].
- Turn the feed handle and catch the quill as it drops out.
- You can now disassemble the quill. There is a piece of plastic tubing on top of the assembly which looks suspiciously like a Taiwanese anti-grease slinger device. Under that is the spindle nut, a nut lock washer and a flat washer – in that order.
- The Nut Lock will have one of the ears bent up to keep the Spindle Nut from turning; using a punch, carefully bend it down so the nut can be removed.
- Now remove the spindle nut (RH thread). Note: the tension on this nut is minimal. It is run down to contact the bearing and turned until one of the tabs on the nut lock can engage a slot. Typically, this arrangement is used to preload a bearing but in this case I think it just keeps the bearing from being displaced.
- Now remove the nut lock and flat washer and set them aside.
- Here is where you will need your hydraulic press. Drive the spindle out of the quill from the top. Once the spindle is out you can tap the bearings out of the quill with a brass punch or hardwood dowel. You will notice the two bearings inside the quill differ; the upper one is smaller – the 6203ZZ – while the lower one is the 6204ZZ. This lower bearing is the same as the paired bearings on the drive sleeve. [Photo 6]
Remove the drive sleeve from the head.
- The drive sleeve [photo 7] is held in place at the top of the drill press head by two “Circlips”, one on top and one underneath the Drive Sleeve. Remove the upper clip by grasping one ear of the clip and slipping a slim screwdriver behind the clip. Carefully work the clip out. The one under the drive sleeve can be left in place.
- Use a hardwood dowel and tap the drive sleeve assembly [photo 8] out from below – that is, stick the dowel into the head from the bottom side and use a dead blow hammer to tap the drive sleeve out toward the top. It is a loose press fit but tap evenly so you don’t cock it as you drive it out.
- Now press the drive sleeve out of the two bearings. Note that you need to position the unit with the threaded part down. Support the bearings and then use a piece of stock smaller than the inner bearing race that bears on the center column of the sleeve so it can be pressed out. The two bearings are separated by a plastic ring that you need to retrieve even if you are replacing the drive sleeve and bearings.
[table id=3 /]
Disassembly is now complete and all parts can be cleaned and inspected.
Assembly is basically the above procedure in reverse.
Use grease sparingly during assembly. You need to grease the spindle but remember that the spindle is moving up and down through the drive sleeve during operation and the belts are subject to flying gobs of grease as this occurs.
- Press the drive sleeve into the two drive sleeve bearings with the plastic ring between them.
- Clean the socket that will receive the drive sleeve.
- Install the drive sleeve assembly into the head. Put a light coat of oil on the outer bearing race of the drive sleeve bearings and push the drive sleeve assembly into place from the top. Try pushing it into place manually; if the bearings align correctly you can push or gently tap the assembly into position. If it won’t go in easily then you can pull it into place using a threaded rod passed through the assembly. Use a scrap of wood or metal below and a washer and nut on top and tighten the nut to pull the assembly down. You only need to get it in far enough to install the upper circlip. Do not distort or damage the lower circlip.
- Install the quill.
- Assemble the quill and spindle with their bearings.
- At the top of the spindle, install the flat washer, the nut lock, and then the spindle nut. Snug the spindle nut then back it off to engage the nearest tab on the nut lock that will engage and bend that up.
- Re-install the plastic tubing. Clean the quill itself, with attention to the teeth on its side and apply a light coat of oil.
- Insert the quill into the head and engage the handle to crank the quill up.
- Install the quill return spring assembly – essentially the reverse of the above. Remember to preload the spring about one turn before locking the nut down. Install the jam nut.
- Re-install the pulley and belts and re-install the head onto the column. Adjust the quill set screw to minimize play but be sure the quill moves freely.
- Re-install the light bulb.
- Install your arbor and chuck and you are … Done!
I would recommend doing a rebuild if you are having run out issues. It’s not hard to do and the cost is more than acceptable (if you don’t count a new chuck). The improvement in performance is significant – run out at the arbor on my drill press is now less than 0.0005″ TIR and that drill bit looks like it’s standing still!
Mikey
2006
Update: It is now February 2010 and the run out at my arbor is still under 0.0005″ TIR despite hard use in a typical hobby machine shop. I believe the use of high quality bearings minimizes wear on the spindle and drive sleeve and help to maintain accuracy. At this rate I may never get to try that angular contact bearing!
Kev, you are right in that a ball bearing can sustain some axial load but they are not meant to do this as a primary function. Axial loads are best handled by tapered roller bearings or angular contact bearings.
Keep in mind that load handling in one direction is true of single row angular contact bearings but double row angular contact bearings will handle loads in both directions. You can also put a single row angular contact bearings at each end of the spindle and it would handle axial loads in both directions. Such is the case for most milling machine spindles that use these bearings.
For a drill press, the primary load is in the downward direction. The forces experienced when you withdraw the drill is relatively light so a single row angular contact bearing at the end of the spindle will be fine, although a double row would be even better if one can be fitted.
The advantage of the angular contact bearing is that it can sustain a significant axial load in the primary direction AND sustain large radial loads at the same time. Ball bearings do not do this nearly as well, nor do they live as long when asked to do it.
Hi, I have a Galaxy 100S Drill press that was made in Taiwan about 25 years ago. The spline on the spindle and the male spline on the drive shaft are worn, but the bearings and quill appear ok. Do you know where I can obtain these replacement parts?
David, I do not know where you can find parts. You can try contacting Rexon in Taiwan; they may know who made your press. I have no way of knowing who that was – sorry.
Great post.. Attractive image! Thank you for your info.. We are Appliance Parts and Supplies with dishwasher parts, dryer parts and more.,…
Thanks for this article, I followed it exactly but the switch on mine was missing. I found an OEM replacement, but have no idea how to wire it. Any chance you could unscrew your switch plate and send me a picture of the back of it connected to the harness please?
Sure thing, Bob. Can you send me an email address so I can send the pics? The software on this site won’t allow me to attach them.
I appreciate the help but I got it figured out. One of the lugs on the back of the switch accepts two of the wires from the harness. When I figured that out, the rest was cake. Thing runs like a champ now ! BTW, I bought this machine at a pawn shop for $40, best deal I’ve gotten in a while! Again, thanks for publishing the project, it really simplified the process for me.
Looking for some help…I have a Craftsman 137.229150 and the rack (that is what it seems to be called) got broke. The tooth strap that allows you to raise and lower the table. I’m looking for a replacement but everywhere I look it says it is no longer available. Does anyone have a hack for this? Thanks!!
Sears Parts no longer has ANY of the parts for this unit.
This is an old post, but I just did mine, which is at least 25 years old. First off, the existing bearings “seemed” OK. I did not measure run out, because you could see it. I replaced them.
Second, you may not need a press. I took my quill to a local machine shop, and the guy proceeded to take a “soft” hammer and tap the spindle a few times and out it popped. So, you may want to try the same thing before heading to a machine shop.
Third, I ended up with the pulley on top of the spindle too high. I think it’s a tight fit there. I just took a plastic hammer and pounded it down till it stopped and it was fine. Maybe I should have used more grease?
Fourth, in my case, the problem is either the chuck or the attached arbor. I can still see wobble after the bearings. I have ordered a new one. You should closely examine your chuck and/or arbor before proceeding.
My runout problem WAS the chuck and/or arbor. I did not go for the pricey ones. Spent about $45 or so at Amazon for chuck and arbor, but it seems to be fine. Having an issue with the quill “jumping” when going up and down. I don’t see anything wrong with the quill grooves or the pinion teeth on the handle. Any ideas here would be useful.
The most likely thing would be a burr or crud on either the quill rack or the pinion gear; there isn’t anything else directly involved. I suppose there can be contact between the quill and the screw that adjusts for side play of the quill. There may be a burr inside that groove. This would be suggested if the jump occurs at the same place every time. Otherwise, I’m stumped.
Following this guide in 2021.
Bearings can easily be found on ebay. A replacement set of Nachi’s (2X 6204ZZ, 1X 6204-2RS, 1X 6203ZZ) costed around $30. I have these on order now.
I found the part numbers for the spindle (10605822) and drive sleeve (10606505) on the Sears website, but of course, they are not available. Mikey had mentioned that the press itself was produced by Rexon in Taiwan, so I just googled the part numbers themselves, and it looks like Rexon has started to produce the same head as a “Jet 2500.” The parts diagrams are identical, and the part numbers are even the same. I went ahead and took the risk and purchased a replacement spindle and drive sleeve on Ereplacementparts, so I will keep you updated on the results.
Excellent! Keep us posted.
The parts finally arrived today.
The drive sleeve had to be put on order from the manufacturer by ereplacementparts. It took nearly a month for it to finally arrive. The spindle is identical. All threads, tapers, and dimensions. Surprisingly, the drive sleeve showed up with bearings installed, albeit the picture showing just the sleeve. It is slightly different, as there is a recess for a plastic cap that’s installed over the top of the bearings, which are paired without the plastic spacer. I don’t quite know what this plastic cap is for, as the spindle is unable to pass through the drive sleeve with the cap on. It pops right off easily.
Up until this point, I had used heat/cold to overcome the lack of a shop press. I used a heat gun to remove the spindle from the quill, remove the bearings from the quill, and remove the bearings from the old drive sleeve. However, the new drive sleeve caused me issues; I had to borrow a neighbors hydraulic press to get them removed. Much easier! I could have simply placed the drive sleeve with its installed bearings into the head, but the bearings did not have a spacer between them and they felt less quality than the replacement Nachi’s
The new spindle bearings went in the freezer for a couple hours before heating up the quill; I was able to hand press the bearings in with little effort. Used the same process with the spindle: spindle in freezer, heated up bearings inside the quill, very easy hand press fit. The new drive sleeve gave me more issues as the temperature difference was not enough to overcome the interference fit; had to use the neighbor’s press again to get them installed with the spacer in the middle. This assembly was placed in the freezer and I heated the head, it dropped right in without issues.
Reassembly was very easy after the bearings were in place! Used some white lithium grease between the quill and feed handle, as well as between the spindle and drive sleeve. Once all buttoned up, I installed a new chuck (went with a cheapo off of Amazon, can replace later) and turned it on.
The result was astonishing. Previously, I could visually see runout at the arbor and at the end of the chuck. Now, it’s virtually motionless. I don’t have a dial indicator to measure runout, but the intent of the rebuild was to get the press into better shape: Mission Accomplished! To test, I had an aluminum part with a M3 snapped screw in the center. The fixed drill press was able to remove the remaining part of the screw without damaging the internal threads of the part!
All in all, I believe I spent around $150 for the replacement parts. This is quite high, but the experience was well worth the expenditure. I hope anyone looking to do this finds this useful; the spindle (10605822) and drive sleeve (10606505) from ereplacements.com worked well.
Thanks for the detailed followup, Knippa. Glad you were able to find the parts and get your drill press running to your satisfaction.
Now that we have you hooked on this machine restoration thing, time to start looking for a lathe! That is a rabbit hole you’ll really enjoy!!
I want to thank you for the article. It’s very timely for me despite its age.
I just purchased a used Craftsman 137.229150 for $100.00. It appears to be in near-new condition, cosmetic surface rust on the column, a bit of rust on exposed cast iron, and no scratches anywhere in the paint, no dents, nothing. Pulleys appear to be original and have no wear. I don’t know if the belts are OEM but they appear new with no visible wear. The seller said his employer gave it to him just to get it out of the shop because it had been sitting in the corner for at least 10 years.
(I’m guessing closer to 20-25 yrs.) He thought it was purchased new for use in a some sort of machine shop coop training program and saw very little use. So, I think it is technically used but actually new. The climate here in Utah County, Utah, is very dry, 25-28 inches of rain per year, average relative humidity is around 20% or less. So that helps with the rust as did its life in a climate-controlled environment. My garage won’t be that kind. I had to remove the head and table for it to fit in the back of the minivan. Other than a bit of polishing and buffing before I put everything together again, it needs nothing.
I don’t have a dial gauge to test run-out—yet. But I will in a few weeks. So, before I bought the drill, I grabbed the spindle and tried to move it sideways, back and forth, etc. It wouldn’t budge. I used an aluminum speed square on the table with the other straight edge near the chuck and spindle. I could see visible wobble for certain on the chuck. I wasn’t certain about the spindle but it “seemed” ok. I’ll test it once I have a dial gauge. At any rate I purchased it with the expectation of replacing the chuck for certain, and perhaps the spindle bearings if the dial gauge shows issues. If I do the latter, your read-out of the required bearings will be invaluable. I’m a fairly competent DIYer and would have figured out the replacement—eventually. You’ve saved me a lot of frustration and research. I’m always appreciative of the shared expertise by those who know more than I do about something. I’m 66 years old, 67 in November. This drill should meet my needs, probably for my lifetime if I take care of it. Anticipated use is mostly woodworking with the occasional bit of metal or plastic here and there.
hi….can someone send me the PDF article with all the pictures…the blog post is missing many pictures. thanks!
tom
I know this is an old post, but I’m hoping someone can help me. I just bought a 137.229150, and I’m trying to replace the chuck because the teeth are so chewed up that they barely catch the chuck key teeth. I have the chuck removal tool, but the arbor and chuck aren’t budging. It’s actually creating gouges in the tool from the top of the arbor and top of the slot.
I’ve sprayed BP Blaster penetrant in it, and so far no luck. My next thought it to either heat it up, or buy the wedges that go between the top of the chuck and the bottom of the spindle.
Any suggestions?
Use heat. A propane torch should provide enough to expand the quill.